Gas generators and cogeneration
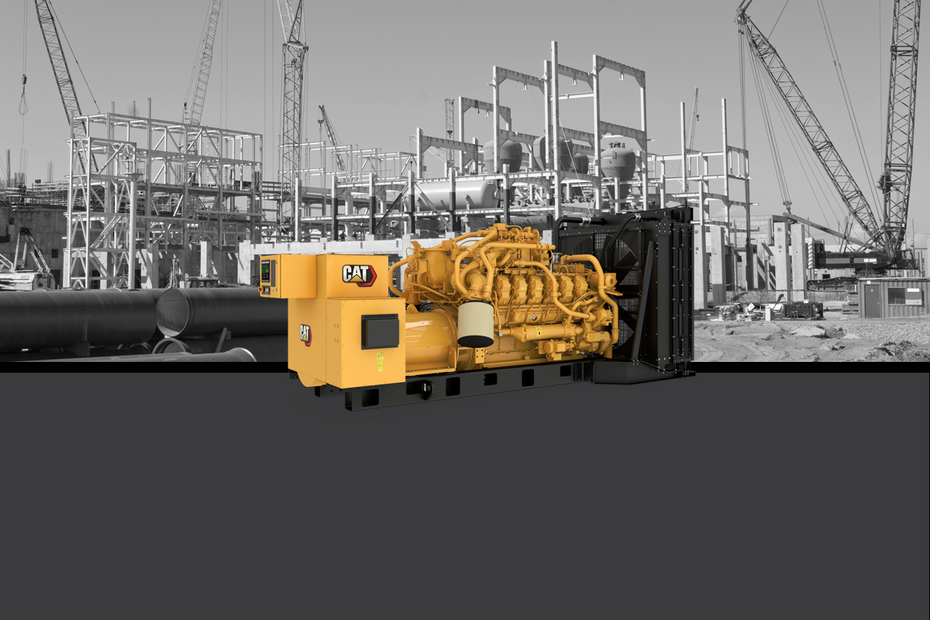
Caterpillar is one of the leading companies in the world, which offers efficient and reliable electric power generating solutions, while maximizing customers' return on investment.
Cat gas gensets are the industry benchmark for reliability and performance. They are manufactured in Caterpillar factories according to ISO 9011 quality standards. Innovative technologies as well as company's vast experience guarantee exceptional quality, reliability and notedly lower maintenance costs.
A full range of Cat gas generator sets, available to utilize natural gas fuel as well as low energy gases, is presented below.
Benefits of Cat gas gensets:
- Robust high speed block design that provides prolonged life and lower owning and operating costs.
- Leading edge technology in ignition system and air/fuel ration control for lower emission and engine efficiency.
- Corrosion resistant components for durability.
- Crankcase breather with air cleaners for mitigating harmful effects from biogas fuel.
- Low-emission designs that meet most worldwide emission requirements.
- Designed for maximum performance on a low pressure biogas fuel supply.
For continuous biogas to electricity, Caterpillar provides one source for your complete project. Avesco Lithuania UAB, as an official dealer in Lithuania can design, istall, service and maintain your generating equipment for the life of the project. We offer:
- low installing cost;
- outstanding fuel efficiency;
- low electricity cost per kWh;
- expeditious delivery of spare parts;
- maintenance and service contracts to fit your requirements
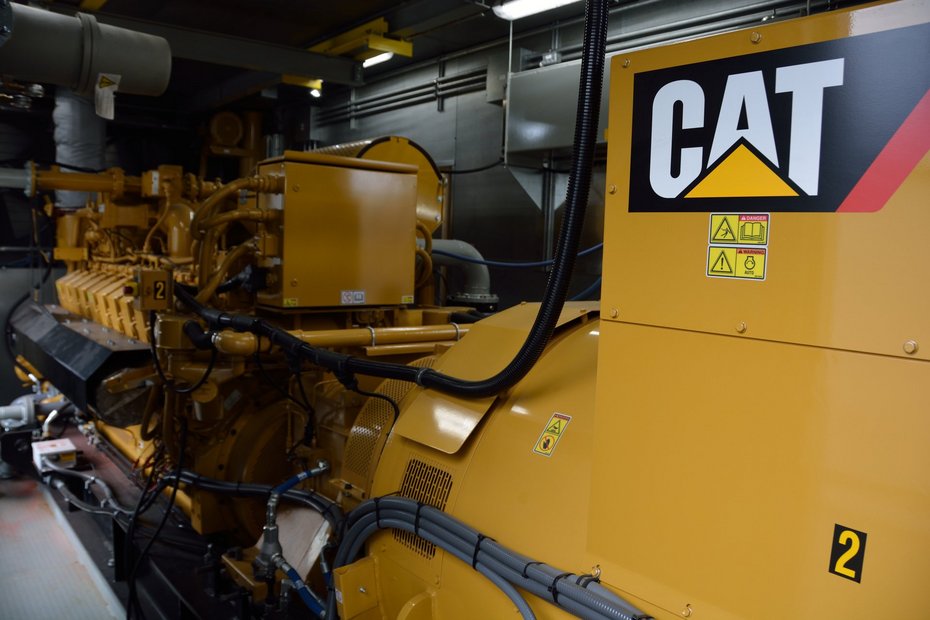
Cogeneration / Chp Solutions
In today’s environment of high gaseous fuel prices, gas engine based Combined Heat and Power installations also called Cogeneration or CHP represent an attractive solution to investors to provide reliable heat and power to their industry or production while maximizing their return on investment.
Combined Heat & Power (CHP or Cogeneration) – is one of the most popular energy-saving technologies. It is the simultaneous and sequential use of power and heat from the same fuel source. When generating electricity, a large amount of heat is produced as a by-product. In traditional power generation methods this is wasted, but a CHP system recycles this heat. In other words, heat recovered from generation is used for heating or cooling, typically with an absorption chiller. This reduces the transmission and distribution losses that occur when fuel is burned, increasing the efficiency of the system. Use of heat for both heating and cooling is known as Tri-generation.
CHP schemes are mainly used by the industrial, commercial and some public sectors – mainly those needing a great deal of heat such as hospitals, universities, leisure centers, offices and retailers. Those industries can be divided in three categories:
- The ones with intensive electric applications: hospitals, offices, shopping malls, industrial processes, logistic centers, etc. Here, the primary purpose for installation is electric power. CHP operates when electricity is required and utilizes load balancing radiators – exhaust circuit bypass.
- The ones with requiring heat and power equally: cement plants, chemical processes, food processing. In this case, both heat and electric power have equal value. Here, CHP are much more complex systems, which require radiators and thermal accumulators.
- And the ones with intensive heat applications: greenhouses, district heating, central steam plants. These applications' primary purpose for installation is heat-related. Such system operates when heat is required and utilizes thermal accumulators-direct connection, which can be hot water or steam circuits.
Advantages of cogeneration plants versus traditional energy generation systems:
- Possibility to generate heat an power simultaneously.
- Possibility to utilize renewable energy sources.
- Reliable energy source – there is no dependance on local utilities.
- Significant reduction of CO2 emission into atmosphere, etc.
Biogas
Model | rev/min | Emission level (NOx) | Power @ 1.0 pf | Efficiency (%) | |||
---|---|---|---|---|---|---|---|
mg/Nm³ | g/bhp-hr | ||||||
kWe | Electric efficiency | Thermal efficiency | Total efficiency | ||||
G3306 | 1500 | 6055 | 16.9 | 68 | 27.9 | 61.5 | 89.4 |
G3306 | 1500 | 6055 | 16.9 | 68 | 27.9 | 61.5 | 89.4 |
G3406 | 1500 | 7613 | 21 | 107 | 28.8 | 60.7 | 89.5 |
G3412 | 1500 | 7051 | 19.9 | 174 | 27.4 | 62 | 89.4 |
CG132-8 | 1500 | 500 | 1 | 400 | 42.8 | 42.1 | 84.9 |
CG132-12 | 1500 | 500 | 1 | 600 | 42.7 | 42.3 | 85 |
CG132-16 | 1500 | 500 | 1 | 800 | 42.8 | 42.3 | 85.1 |
G3516A | 1500 | 500 | 1 | 1041 | 31.1 | 47 | 78.1 |
G3516A+ | 1500 | 500 | 1 | 1105 | 36.8 | 41.5 | 78.3 |
CG170-12 | 1500 | 500 | 1 | 1200 | 42 | 43.8 | 85.8 |
CG170-16 | 1500 | 500 | 1 | 1560 | 41.7 | 43.9 | 85.6 |
G3520C | 1500 | 500 | 1 | 1984 | 39.4 | 41.4 | 80.8 |
CG170-20 | 1500 | 500 | 1 | 2000 | 42.9 | 43.3 | 86.2 |
CG260-16 | 1000 | 500 | 1 | 3770 | 42.8 | 39.5 | 82.3 |
Natural Gas
Model | rev/min | Emission level (NOx) | Power @ 1.0 pf | Efficiency (%) | |||
---|---|---|---|---|---|---|---|
mg/Nm³ | g/bhp-hr | ||||||
kWe | Electric efficiency | Thermal efficiency | Total efficiency | ||||
G3306 | 1500 | 10607 | 26.2 | 86 | 31.9 | 57.5 | 89.4 |
G3306 | 1500 | 10193 | 25.6 | 115 | 31 | 55.8 | 86.8 |
G3406 | 1500 | 11293 | 27.5 | 126 | 31.9 | 57.5 | 89.4 |
G3406 | 1500 | 846 | 25 | 166 | 32.2 | 50.2 | 82.4 |
G3412C | 1500 | 500 | 2 | 374 | 33.7 | 50.4 | 84.1 |
CG132-8 | 1500 | 500 | 1 | 400 | 42.3 | 45.2 | 87.5 |
CG132-12 | 1500 | 500 | 1 | 600 | 42 | 45.8 | 87.8 |
CG132-16 | 1500 | 834 | 1 | 800 | 42.3 | 45.2 | 87.5 |
G3516 | 1500 | 500 | 2 | 983 | 34.8 | 48.3 | 83.1 |
G3512E | 1500 | 500 | 1 | 1016 | 41.4 | 44.7 | 86.1 |
G3516B | 1500 | 500 | 1 | 1068 | 37.1 | 47.8 | 84.9 |
CG170-12(K) | 1500 | 500 | 1 | 1125 | 40.9 | 45.6 | 86.5 |
CG170-12 | 1500 | 500 | 1 | 1200 | 43.6 | 43.3 | 86.9 |
G3512E | 1500 | 500 | 1 | 1211 | 42.2 | 44.2 | 86.4 |
CG170-16(K) | 1500 | 500 | 1 | 1500 | 40.9 | 45.7 | 86.6 |
CG170-16 | 1500 | 500 | 1 | 1560 | 43.2 | 43.8 | 87 |
G3516E | 1500 | 500 | 1 | 1603 | 41.6 | 44.4 | 86 |
G3516C | 1500 | 500 | 1 | 1603 | 40 | 46.5 | 86.5 |
G3520C | 1500 | 500 | 1 | 1991 | 40.1 | 46.3 | 86.4 |
CG170-20 | 1500 | 500 | 1 | 2000 | 43.7 | 43.2 | 86.9 |
G3516H | 1500 | 500 | 1 | 2027 | 44.7 | 41.8 | 86.5 |
G3520E | 1500 | 500 | 1 | 2022 | 41.5 | 45.3 | 86.8 |
G3520H | 1500 | 500 | 1 | 2519 | 45.4 | 40.9 | 86.3 |
CG260-12 | 1000 | 500 | 1 | 3333 | 43.9 | 42.6 | 86.5 |
CG260-16 | 1000 | 500 | 1 | 4300 | 44.1 | 42.7 | 86.8 |